from CoTec Holdings Corp. (isin : CA22165A1021)
HyProMag USA Feasibility Study Demonstrates Robust Economics and the Opportunity to Develop a Major New, Domestic Source of Recycled Rare Earths Magnets for the United States
LONDON, UK and VANCOUVER, BC / ACCESSWIRE / November 25, 2024 / CoTec Holdings Corp. (TSXV:CTH)(OTCQB:CTHCF) ("CoTec") and Mkango Resources Ltd. (AIM:MKA)(TSX-V:MKA) ("Mkango") are pleased to announce the results of an independent Feasibility Study (the "Feasibility Study") for HyProMag USA, LLC, ("HyProMag USA or the Project") on the development of a state-of-the art rare earth magnet recycling and manufacturing operation in the United States.
The Project is underpinned by the patented Hydrogen Processing of Magnet Scrap ("HPMS") technology developed at the University of Birmingham Magnetic Materials Group and being commercialized by HyProMag in the United States, United Kingdom and Germany. The HPMS process recovers neodymium iron boron ("NdFeB") permanent magnets from end-of-life scrap streams in the form of a demagnetized NdFeB metallized alloy powder for remanufacture into recycled NdFeB magnets with a significantly reduced carbon footprint, and has major competitive advantages versus other magnet recycling methods using chemical processes.
Sintered NdFeB magnets will be produced in the United States using materials sourced in the United States, contributing to security of NdFeB permanent magnet supply and enabling economical, traceable, domestic U.S. production of recycled NdFeB magnets (DFARS compliant [1] ) supporting the defense, aerospace, automotive, medical science, hyperscale data centers, robotics, and energy transition industries.
Highlights
Positive Feasibility Study results for state-of-the art rare earth magnet recycling and manufacturing operation in the United States (the "Project"), with a central Dallas Fort Worth ("DFW"), Texas hub supported by two pre-processing spoke sites in the eastern and western regions of the United States:
US$262 million post-tax Net Present Value (NPV) [2] and 23% real internal rate of return (IRR) based on current market prices [3],[4]
US$503 million post-tax NPV [2] and 31% real IRR based on forecast market Prices [5],[4]
Low all-in sustaining Cost (AISC) of US$19.6 per kg of NdFeB product which compares to current weighted average market prices of US$55 per kg of NdFeB products, the latter reflects underlying prevailing low rare earth prices with significant scope for price recovery
Expansion potential with the inclusion of a third HPMS vessel within three years following commissioning for an additional capital cost of approximately US$7 million
A 3D fly through of the Project feasibility design can be found at HyProMag USA Facility Flythrough
Production of 750 metric tons per annum of recycled sintered NdFeB magnets and 291 metric tons per annum of associated NdFeB co-products (total payable capacity - 1,041 metric tons NdFeB) over a 40 year operating life
Up-front capital cost of the Project is US$125 million (inclusive of a 10% contingency margin and Class 3 AACE estimated detailed design study and engineering costs) over a 1.7 year construction phase
Payback [6] is achieved at current market prices in 3.9 years at a profitability index ("PI") [7] of 2.1, at forecast market prices payback is achieved in 3.1 years at a PI of 4.0
First Revenue targeted in Q1 2027 with a Notice to Proceed ("NTP") expected in mid-2025 following completion of Detailed Engineering Design and Value Engineering phase, which will commence shortly and include:
Evaluation of significant opportunities to optimize construction and operational efficiency, and to reduce capital expenditure and operating costs, as well as to expand production
Parallel product and operational testing in the UK at the University of Birmingham Magnetic Materials Group ("MMG") pilot plant and in conjunction with HyProMag commercial developments in UK and Germany
Completion of commercial arrangements with potential feed supply and product off taker - discussions with several potential parties underway
Continued discussions with federal, state and municipal governments, in relation to financing opportunities and other economic incentives including carbon price premiums which could improve economics
Project will help secure the re-vitalization of NdFeB magnet production in the United States with the creation of approximately 90 jobs across Texas, South Carolina and Nevada
Minviro Limited [8] has been commissioned to complete an ISO-14067 compliant "Product Carbon Footprint" analysis of sintered materials by the end of Q4 2024 using the results of the Feasibility Study
HyProMag USA is targeting 10% of U.S domestic demand for NdFeB magnets within five years of commissioning - design is modular, can be replicated and accelerated to facilities in eastern and western United States
The Feasibility Study was undertaken by a multidisciplinary team appointed by CoTec and Mkango and led by independent engineers, Canada-based BBA USA Inc. ("BBA") and U.S. based PegasusTSI Inc. ("PegasusTSI") with other independent experts and support from University of Birmingham, HyProMag Ltd and HyProMag GmbH
Julian Treger, CoTec CEO commented: "We are very pleased with the results of the independent Feasibility Study, which further demonstrates the advanced commercialization potential of HyProMag's technology. HyProMag has the capacity to provide the United States with a secure domestic source of permanent magnets to accelerate the revitalizing of U.S. magnet production, metallization, and skills development, a strategic priority for the U.S. Government."
"The Detailed Engineering Design phase is expected to deliver further cost savings and design improvements which should enhance the project's metrics even further. The company is now focused on securing funding from the U.S. Government, financing, off-take and feed supply. The end-to-end process of recycling end-of-life NdFeB magnets into new sintered NdFeB magnets is supported by the Minerals Security Partnership [9] which aims to accelerate the development of secure, diverse, and sustainable supply chains for critical minerals. We are very excited the business can be used as a platform to create a market leading position for low cost, low carbon magnet recycling."
Will Dawes, Mkango CEO commented: "This is a major milestone for HyProMag, further validating the HPMS technology and opportunity to roll-out into the United States. Our strategy to develop rare earth magnet recycling and manufacturing hubs in the United States, UK, Germany and, in the future, Asia, is aligned with the evolving geopolitical environment through the development of more robust rare earth supply chains for the respective domestic markets, while catalyzing new centers of excellence in magnetic materials and cross-fertilization of skills across jurisdictions and between industry and academia."
Ownership
HyProMag is 100 per cent owned by Maginito Limited ("Maginito"), which is owned on a 79.4/20.6 per cent basis by Mkango and CoTec. HyProMag USA is owned 50:50 by CoTec and Maginito.
Detailed Engineering Design and Value Engineering
Following completion of the Feasibility Study, the Project will now proceed to the Detailed Engineering Design and Value Engineering phases.
The Detailed Engineering Design will include the completion of sufficient engineering design works to support a AACE Class 1 capital estimate, as well as final site selection is expected to be completed in H1 2025 and site permitting targeted for completion by Q4 2025 in line with the initial project schedule. This targets initial revenue in Q1 2027. Environmental and permitting studies are supported by U.S. based Weston Solutions, Inc. Following completion of the Detailed Engineering Design, a NTP decision will be taken mid-2025 as to whether HyProMag USA will proceed with the construction of the Project.
Detailed Engineering Design will focus on optimization of construction and operational efficiency and identifying potential improvements that could lead to substantial capital expenditure and operating cost savings. It will also encompass definition and optimization of the third HPMS expansion case. In parallel with Detailed Engineering Design and Value Engineering, product and operational testing will continue in the UK at the University of Birmingham Magnetic Materials Group (MMG) pilot plant in conjunction with HyProMag commercial developments in UK and Germany.
The data used to develop the processing flowsheet is based on historical test work and magnet production at the HPMS Pilot vessel through the MMG at the University of Birmingham in the UK, which developed the HPMS technology being commercialized by HyProMag. Additional test work will be undertaken to further optimise the flowsheet, particularly in the HPMS operations. The capital and operating costs will be refined in line with the expected improvements to the overall process flowsheet, which will influence long-lead capital items. A formal request for proposal ("RfP") process will also be undertaken as part of the Detailed Engineering Design phase of the Engineering, Procurement, Construction Management ("EPCM") contract to solicit final vendor quotes to improve the accuracy of the capital cost estimate. The detailed engineering considers a "one contractor" approach who is appointed to develop and build the complete process plants.
In parallel, HyProMag USA is working towards securing potential U.S. Government funding, U.S. State financial grants and incentives and strategic partnerships with U.S. companies. Significant progress was achieved in the areas of feed supply and recycled NdFeB magnet offtake during the Feasibility Study and the Project is now able to proceed with securing long term commercial agreements.
CoTec is responsible for funding the Detailed Engineering Design, Value Engineering and the project development costs. Funding provided by CoTec would be in the form of shareholder loans to HyProMag USA.
The Feasibility Study
The Project will use a "hub-and-spoke" operational model, with the central, DFW, Texas hub supported by two pre-processing spoke sites in eastern and western United States.
The Feasibility Study is based on the development of a state-of-the-art 40-year magnet manufacturing facility in DFW, Texas, capable of producing up to 750 metric tons payable of sintered NdFeB magnets and 291 metric tons of associated NdFeB co-products (total payable capacity - 1,041 metric tons NdFeB) annually. First Revenue is targeted in Q1 2027 with a Notice to Proceed (the "NTP") expected in mid- 2025 following completion of the Detailed Engineering Design phase.
The Feasibility Study demonstrates robust economics at Current Prices and indicates a significant upside based on the forecast recovery in the rare earths market. Based on a current market prices, derived from current market pricing for the various products, the Feasibility Study indicates a post-tax NPV[ 10] of US$262 million and real IRR of 23% (pre-tax NPV US$343 million and real IRR of 27%) at a real discount rate of 7.0%. Based on forecast market prices, the Feasibility Study indicates an post-tax NPV of US$503 million and real IRR of 31% (pre-tax NPV of US$647 milliion and real IRR of 36%) at a real discount rate of 7.0%.
The up-front capital cost of the Project is US$125 million (inclusive of a 10% contingency margin and Class 3 AACE [11] estimated detailed design study and engineering costs). The current market price payback [12] is achieved in 3.9 years at a profitability index ("PI") of 2.1 [13] , whilst at Forecast Prices, payback is achieved in 3.1 years at a PI of 4.0.
The Project has a low all-in Sustaining Cost of cost production at US$19.6 per kg of NdFeB which compares to current market prices of US$55 per kg of NdFeB product.
Production at the hub facility is readily expandable with the inclusion of a third HPMS vessel within three years following commissioning for an additional capital cost of approximately US$7 million - the third HPMS vessel is expected to supply excess HPMS NdFeB payable powder to the U.S market for the developing domestic magnet production industry.
The main products are sintered magnet materials split between blocks and finished magnets at magnet grades that have been previously demonstrated at the University of Birmingham pilot facility [14] . These include DFARS compliant products and will support a closed loop system in the United States whereby end-of-life U.S.-sourced NdFeB magnets are recycled into new magnets via HyProMag's short-loop process.
The Project will therefore provide a long-term, traceable source of permanent magnets for U.S industry including applications for electric vehicles, wind turbines, and many electronic devices critical for U.S. critical mineral supply chains and the energy transition. Furthermore, the Project will help secure the re-vitalization of NdFeB magnet production in the United States with the creation of approximately 90 jobs in relation to magnet manufacturing, further catalyzing the developing rare earth industry ecosystem in Texas and the cross fertilization of skills, training and R&D between the United States, UK and Europe.
The key Feasibility Study metrics of the Project are summarized in Table 1. The Feasibility Study did not incorporate prospects for potential economic support from governments, funding opportunities, or other economic incentives which could improve the economics and influence a future updated detailed design engineering and investment decision.
Table 1: Feasibility Study Key Metrics in US$
Assumptions | Unit | Current Prices | Forecast Prices |
Project Duration (Life of Asset) | Years | 40 | 40 |
Average annual system capacity | Metric tons NdFeB per annum | 1,147 | 1,147 |
Average annual payable production | Metric tons NdFeB per annum | 1,041 | 1,041 |
Average total payable Sintered Magnets | Metric tons NdFeB per annum | 750 | 750 |
Average total payable co-products excluding residual scrap | Metric tons NdFeB per annum | 291 | 291 |
Economic Assumptions | |||
Weighted average price (Life of Asset) | US$/Kg | 55 | 94 |
Capital Cost | |||
Construction period | Years | 1.7 | 1.7 |
Initial CAPEX (excl. closure and sustaining) | US$ million | 125.3 | 125.3 |
Sustaining CAPEX | US$ million per annum | 0.21 | 0.21 |
Operating cost per metric ton | |||
Transport Cost (Spoke to Hub) | US$/kg NdFeB | 0.46 | 0.46 |
Royalty Cost | US$/kg NdFeB | 0.23 | 0.69 |
TOTAL AISC [15] LIFE OF ASSET | US$/kg NdFeB | 19.63 | 31.86 |
Basis of Feasibility Study
Feasibility design and economic analysis thereof was undertaken for the Project. A system capacity of 1,147 metric tons per annum has been used as a basis for the Feasibility Study.
The process begins with scrap pre-processing at the spoke facilities located in the eastern and western United States, where electronic and industrial scrap containing NdFeB magnets is pre-processed, sorted, and prepared for HPMS at the hub. This pre-processed material is then transported to the central hub in DFW for HPMS and magnet manufacturing.
At the DFW hub in Texas, the HPMS system uses hydrogen to extract NdFeB powder from the scrap material in a series of controlled reactions that occur at near atmospheric pressure. This method minimizes energy consumption and reduces environmental impact compared to conventional extraction methods. Following extraction, the NdFeB alloy powder undergoes conventional magnet manufacturing to produce high-performance magnets that meet industry standards.
Economic analysis has been performed in accordance with the process design and schedule, metallurgical testing, and product payability analysis developed in the study, and the estimates and analyses therein have been prepared to a Class 3 AACE Feasibility level.
Processing Design
The proposed plant is based on both historical, and 2022 to 2024 pilot test work at the University of Birmingham together with the approximate US$100 million of historical R&D expenditure and the significant know-how and related intellectual property for HPMS.
HyProMag USA will produce NdFeB permanent magnets in the United States using recycled end of life NdFeB magnets embedded in electronic and industrial scrap as the source material. The HPMS process liberates embedded rare earth permanent magnets, in the form of a demagnetised NdFeB powder, from any electrical drive, be it including hard disk drives ("HDD"), electric motors, MRI magnetic units, speakers and other end-of-life assemblies containing NdFeB, enabling recovery of the NdFeB whilst leaving behind the associated casing materials. These casing materials are recovered and sent to any suitable scrap recycling plant for processing. The recovered NdFeB magnet material can be fed back into any point in the rare earth supply chain, the preferred and principal route for HyProMag being short-loop magnet manufacturing which is facilitated by HPMS. In the short-loop magnet manufacturing process, the recovered NdFeB magnet material is treated and reformed into blocks that can then be shaped and magnetized for use in equipment requiring permanent rare earth magnets of the NdFeB composition. Any scrap material produced from the shaping of the magnet blocks will be recycled for use within the plant or sold to third parties. The only waste products from the process are the casing materials housing the rare earth magnets, which are recycled, and minor discharges of steam and inert gases.
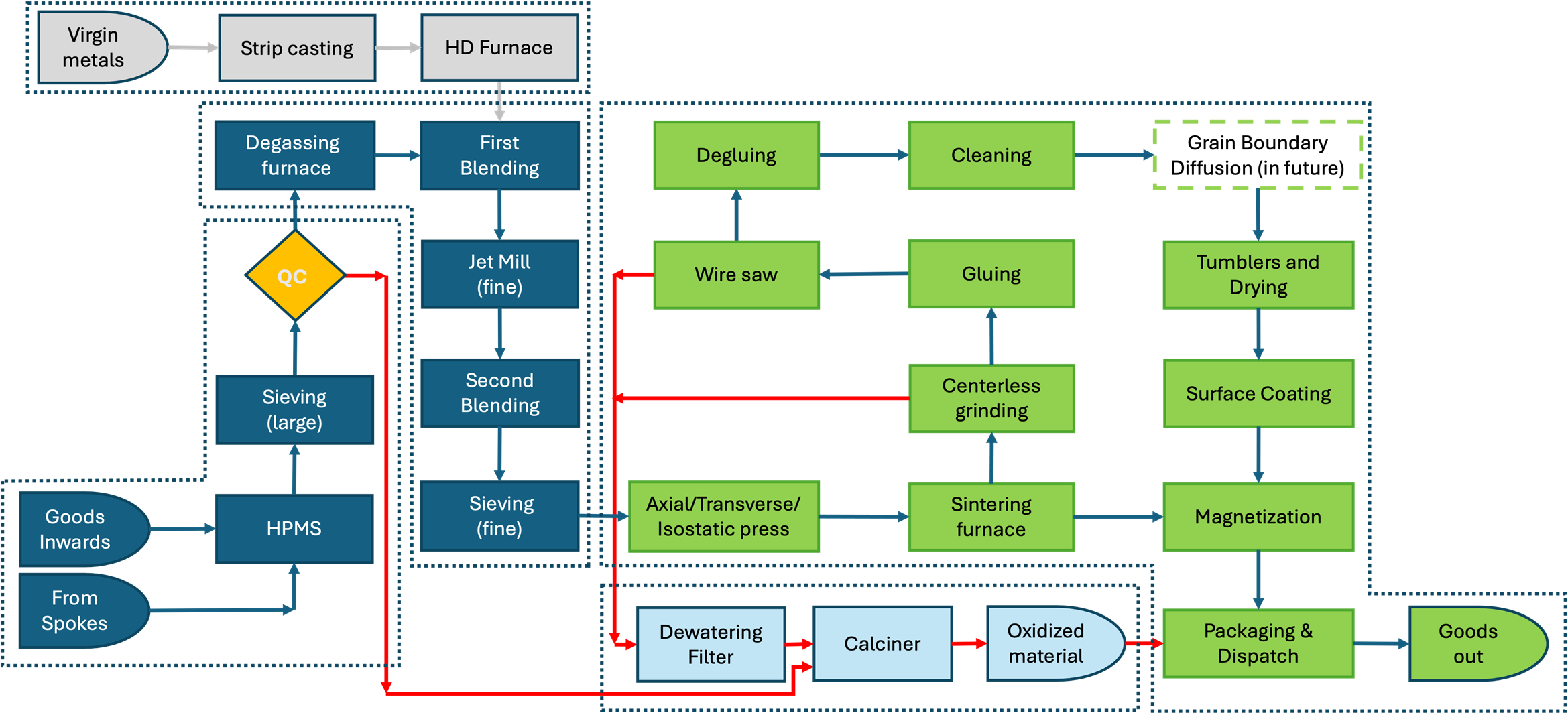
Figure 1: A simple Block Flow Diagram of the magnet recycling and production operation
Pre-Processing technology
Maginito and Inserma Anoia S.L ("Inserma") have entered into a binding and exclusive agreement to collaborate on the optimization, commercialization and roll-out of pre-processing technologies for HyProMag in the United Kingdom, Germany, the United States and other regions. The technologies autonomously pre-process scrap such as hard disk drives to remove the NdFeB magnet containing component which can be processed via HPMS to deliver purified alloy powder on a very large scale.
The latest mobile Inserma unit for HDD can be co-located at hyperscale data centers, shredding, recycling or HyProMag facilities. These Inserma units rapidly remove (at <3 seconds per HDD) the Voice Coil Motor ("VCM") containing the rare earth magnet, providing a highly concentrated feed for subsequent HPMS by HyProMag - the simultaneous removal of the center spindle also facilitates downstream shredding of the rest of the HDD. A 3D flythrough of the Inserma units both in the HyProMag USA facility and also within a United Sates hyperscale data center can be found at HyProMag USA with Inserma HDD Pre Processing Fly Through , Data Center with HyProMag USA + Inserma Technology
The goal of the collaboration is to enable deployment of hundreds of pre-processing units, across multiple jurisdictions, providing pre-processing solutions for a range of end-of-life applications, including HDDs, loudspeakers and electric motors, and generating feed for HyProMag's short loop rare earth magnet recycling process.
Project Site, Infrastructure and Services
Site selection was focused on locating a site in DFW, Texas for the hub. DFW was identified as a suitable location to build the magnet recycling operation based on its central location in the U.S., its sizable e-waste recycling activities, proximity to national rail roads and interstate highways and ease of doing business there. DFW also has other existing and developing magnet and rare earth related businesses in the area.
A selection criteria approach was used to determine potential site locations within the DFW area. The potential site is approximately 100,000 square feet in area, 36 feet in height and utilizes a pre-existing factory storage unit with basic utilities fully installed. The Project design assumes the site will be secured through long term leases in Q1 2025.
The logistics for the project include two main satellite spokes: Satellite Spoke 1, potentially located in Las Vegas, or Reno, Nevada and a Satellite Spoke 2, potentially located in South Carolina. The transportation process from each Satellite Spoke to the hub employs intermodal (truck and rail) transportation.
Power supply will be provided through local utility providers. The current Project design is assuming grid sourced power, however where possible the Project will contract renewably sourced power when it is available.
Supply of Hydrogen, Nitrogen, and Argon at the DFW hub will be provided through specialized companies which provide industrial gases in liquid form. These gases will be delivered and stored on-site in dedicated tanks equipped with vaporizers to ensure the conversion from liquid to gas as needed for the operations in a "over the fence" solution.
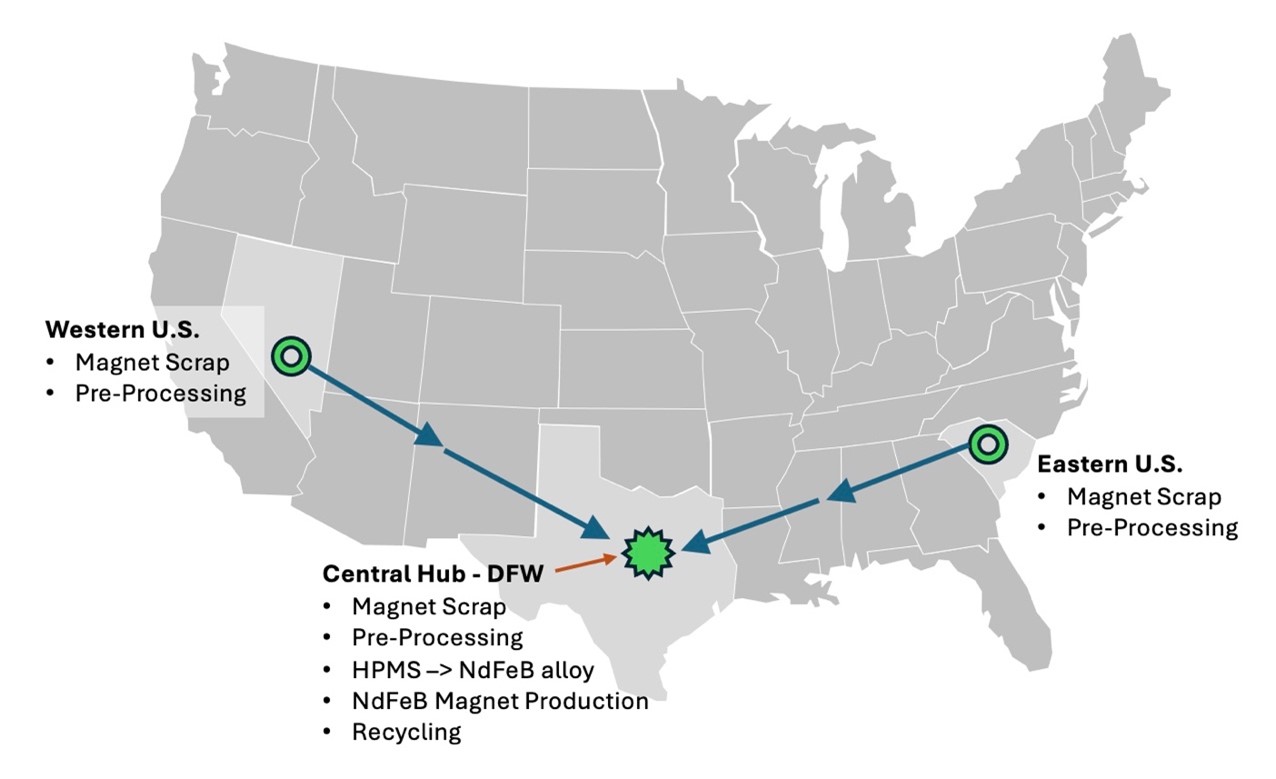
Figure 2: Map of the United States showing planned locations of HyProMag USA's operations and functions.
Capital Costs
Initial capital expenditure (CAPEX) costs for the Project are based on a system capacity of 1,147 metric tons per annum with a nominal payable production capacity of approximately 1,041 metric tons per annum of which 750 metric tons per annum are sintered blocks and finished magnets. CAPEX costs are estimated at US$125 million, including EPCM costs, future Detailed Engineering Design study costs and a 10% contingency.
Sustaining capital over the life of asset (40 years) is estimated at US$9.4 million. Closure cost is estimated at $1M resulting in total life of asset CAPEX cost of US$134.8 million.
Table 2: Capital Costs
Description | US$ (M) |
Hub Plant | 95.0 |
Spoke Pre-Processing | 6.0 |
Indirect Costs (DE Study and EPCM) | 13.5 |
Estimated Sub-Total Cost | 114.5 |
Contingency 10% | 10.9 |
Total Estimated Initial CAPEX | 125.4 |
Sustaining (over life of asset) | 8.4 |
Closure cost | 1.0 |
ESTIMATED TOTAL CAPEX OF LIFE OF ASSET | 134.8 |
Operating Costs
The operating costs include manpower to run the overall operations, power and utilities, materials handling, scrap feed, transport of the scrap materials from the Spoke pre-processing sites to the Hub in DFW, Texas and G&A.
Table 3: Operating costs
Area | US$/kg (current prices) [16] | US$/kg (Forecast Prices) [ 4] |
Pre-processing - Spokes x2 | 1.84 | 1.84 |
Processing - Hub (includes feed supply) | 16.23 | 28.00 |
Transport from Spoke to Hub | 0.46 | 0.46 |
G&A | 0.67 | 0.67 |
Royalty | 0.23 | 0.69 |
ESTIMATED TOTAL AVE. OPEX US$/kg (LIFE OF ASSET) | 19.43 | 31.66 |
Economic Analysis and Sensitivity Analysis
Table 4: Economic Results
Economic Assumptions | Unit | Current Prices | Forecast Prices |
Weighted average price (Life of Asset) | US$/kg NdFeB | 55 | 94 |
Revenue (Life of Asset) | US$M | 2,325 | 3,941 |
EBITDA (Life of Asset) | US$M | 1,528 | 2,642 |
Pre-Tax NPV at 7% discount rate | US$M | 343 | 647 |
Pre-Tax real IRR | % | 27% | 36% |
Post-Tax NPV 7% discount rate | US$M | 262 | 503 |
Post-Tax real IRR | % | 23% | 31% |
Payback | years | 3.9 | 3.1 |
PI | 2.1 | 4.0 |
A sensitivity analysis was performed whereby initial infrastructure capital cost, annual operating costs and product selling price were individually varied between +/-15% to determine the impact on Project IRR and NPV between 0 and 10 % discount rates.
Results are presented in Table 5 and 6. The project financials are most sensitive to the product selling price followed by operating costs and finally initial capital expenditures.
Table 5: Sensitivity Analysis (US$, Million, Post Tax) - Current Prices
Base Case | CAPEX | Current prices | LOA OPEX | |||||
15% |